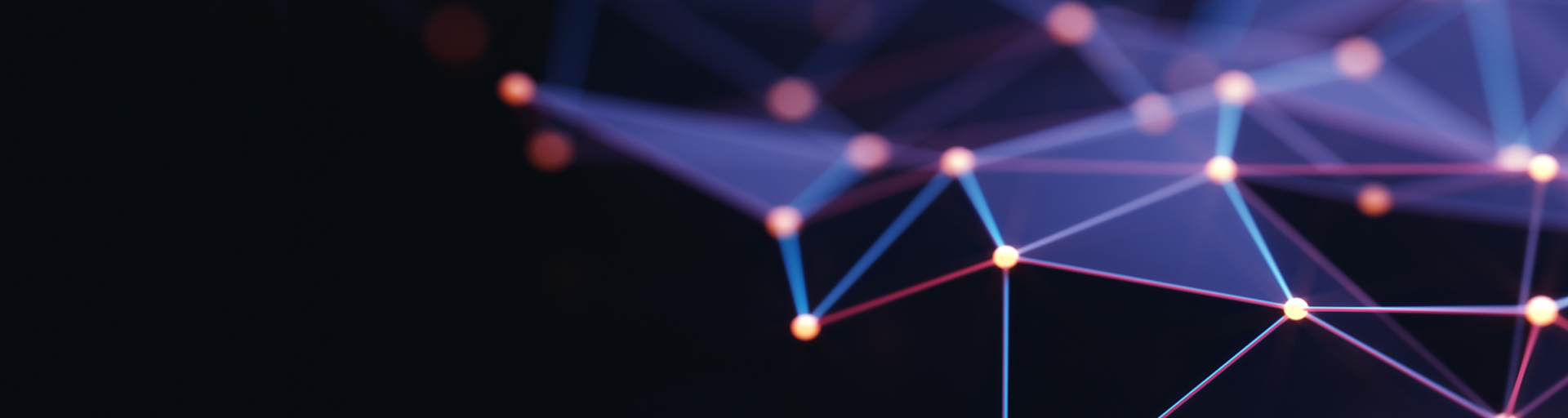
Dynamic 3i - The ERP to Manage Your Manufacturing Business
From raw materials management to production, manage your manufacturing process with Dynamic 3i ERP
Bill of Materials and Routings
Get complete clarity on the raw materials and labour manufacturing your products.
To determine production times and costs quickly and easily, you can facilitate all items on your bills of materials, including raw materials, sub-assemblies, service goods, sub-contract, and more.
Delivering you the benefits to:
Eliminate shortages and manage material requirements with accurate scrap rates and revision history.
Easily define multi-level Bills of Materials.
Track the entire chain of raw material usage, allowing for accurate lot control and facilitating data for defects and recalls.
Forecasting and Planning
Use forecasts to get an outlook on future production requirements and drive your production planning process to ensure you always have the goods to meet your customers' needs.
Giving you the ability to:
Use Sales Forecasts that are blended with actual demand to determine how much to make and when.
Use Production Forecasts to make firm production targets.
Get the complete picture with the Master Production Schedule for accurate demand and supply.
Requirements Planning
Deliver the optimal output for your clients and maximize profits with precise resource and manufacturing planning requirements.
Get data on all your requirements, including run times, customer demand, materials, and labour, and use that data to develop your optimal data-driven production and purchasing plan.
Run Master Production Schedule Explosion in simulated or live scenarios.
Implement scheduling that can drive actual demand and forward-looking forecasts.
Suggest the optimal purchases and work order quantities and start dates.
Capacity Planning
Optimize your manufacturing capacity to ensure that you always meet your customer's manufacturing commitments with capacity planning.
Properly plan and resolve bottlenecks with materials and labour with complete visibility on where capacity exists and where you have overloaded your capacity.
Giving you the benefits of:
Automatically analyzing work orders and work centre capacities to generate detailed reports.
A full view of all inputs into production, labour time, and machine time.
Viewing lead time for individual products.
Production Control
Reasonable production control means you don't incur costs associated with inaccurate production inputs.
Have complete visibility for lot control, raw material usage, and variances to inventory and bills of material.
Allowing you to:
Reduce reliance on data entry and improve accuracy through automated loading of production inputs.
View MRP explosions and generate work orders automatically or manually for current and future work.
Generate manual work orders with information on your existing demand pipeline.
Cost Control
Accurately price your products and ensure profitability when going to market by knowing the total costs of every component in your chain of production.
See detailed product costs based on current raw material costs, and get the big picture to pivot your manufacturing if any of your input costs change.
Giving you visibility to:
Break down each manufacturing stage, including component-level, assembly, labour, and overhead costs.
Simulate modelling to estimate impacts from changing any cost component in the manufacturing process.
Build and summarize comprehensive reporting for informed decision-making for the future.
Dashboards & DYNAMIC Reports
Get the right information to the right decision makers. Our interactive dashboards gives users the power to customize the depth and breadth of reports from Dynamic 3i.
Getting complete visibility via:
Charts, graphs and interactive reports are provided for each role or department
Customized reports and share with colleagues in a variety of formats, including spreadsheet, PDF, or HTML.
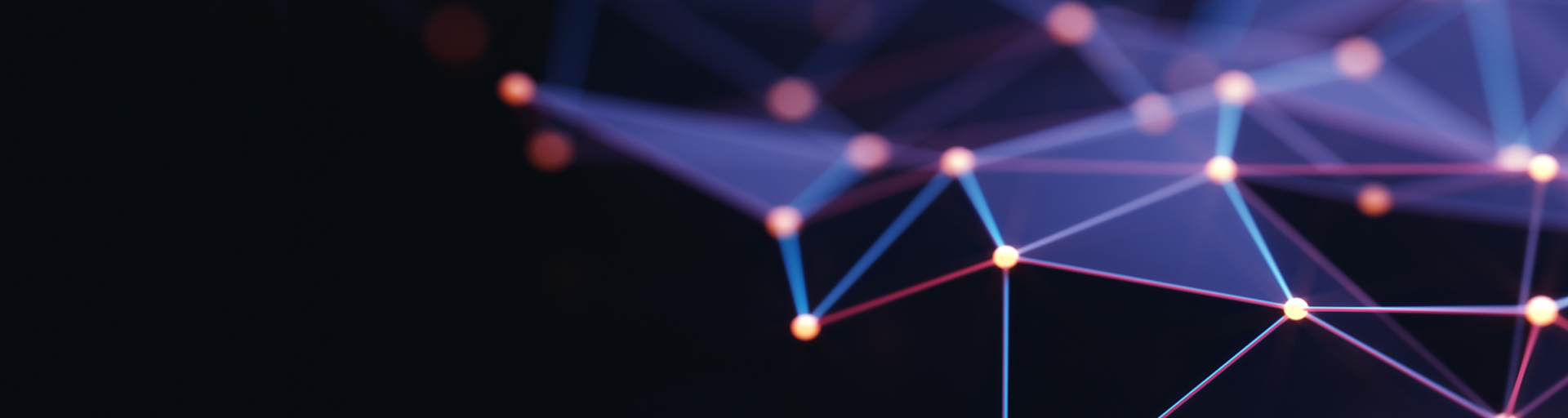
“Dynamic 3i helped us automate 30% of our operations, freeing our staff to take on more important strategic work”
Optional Add-Ons
Preventative Maintenance
Ensure you can always meet customer commitments by preventing unintended equipment downtime and breakdowns that grind production to a halt.
Automatically track asset maintenance schedules that are integrated with other SDC modules.
Allowing businesses to:
Track time, materials, and tools spent on maintenance jobs.
Leverage asset data from other SDC modules to be proactive on asset maintenance.
Quality Control
Your customers trust you to produce products of the highest quality every time.
Manage every process of your quality control, from government regulatory requirements to internal testing plans, with a single module.
This will give complete visibility to:
Track raw material and finished goods standards, and track defect rates as a result of an issue in the supply chain.
Set up quality control tests using customized workflow sequences.
Track historical results to pinpoint origins of quality control issues.
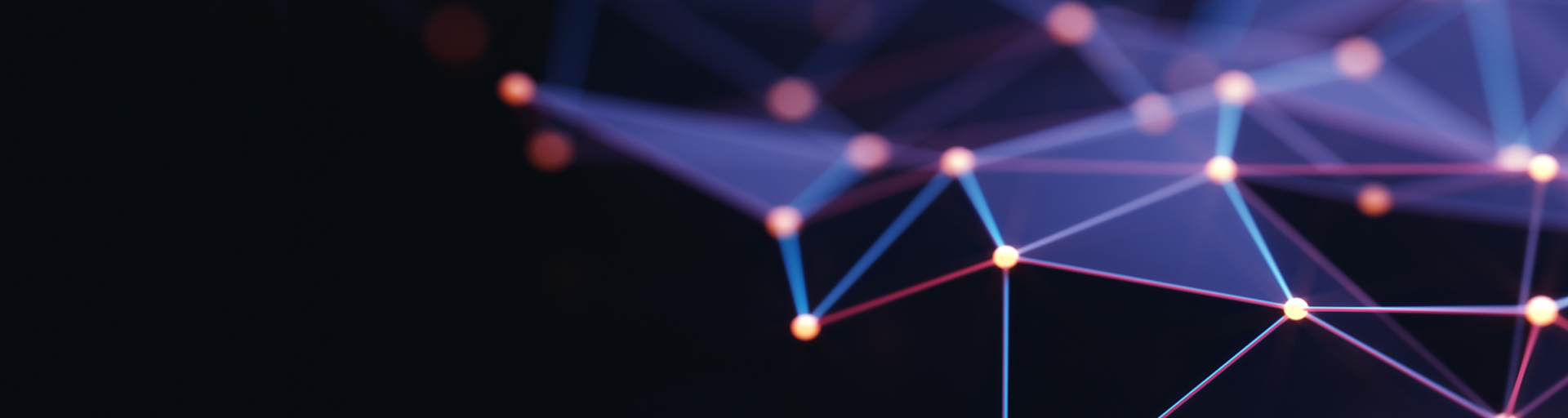